When it comes to international trade and sourcing products from China, making sure they comply with the agreed-upon specifications and quality standards is really important. One key part of checking quality is doing a Pre-shipment Inspection (PSI), standing out as the final check for buyers. This guide explains why PSI matters and offers clear steps for a successful inspection, ensuring a smooth sourcing process.

All inspections are essential in the quality control process, but the Pre-shipment Inspection, commonly referred to as the “PSI,” holds a unique position. By thoroughly examining goods before they leave the manufacturer’s facility, PSI helps reduce the risk of receiving defective or non-compliant products.
The objective of the PSI is to validate that the goods you have ordered have been manufactured in strict accordance with the specifications you provided to the factory.
What sets the PSI apart is its timing – it occurs when the product is fully completed and packed. In essence, what you see during the PSI is precisely what you receive; there is no room for last-minute changes by the factory.
This inspection serves as the buyer’s last line of defense, ensuring that any quality issues are identified before the goods are shipped. Discovering such issues post-PSI can result in major complications for all parties involved.
The Quality Assurance process follows the principle that “prevention is better than cure.” Success is best achieved through collaborative efforts between buyers and sellers. Factories have a vested interest in ensuring a flawless PSI because it guarantees client satisfaction, on-time shipment, and eliminates additional costs related to reworking products. Ideally, all shipments should pass the PSI, indicating that the quality control process has been diligently managed from start to finish.
How to Perform a PSI
Executing a PSI effectively involves careful planning and coordination. Here’s a step-by-step guide to follow the PSI process:
1. Review Specifications:
- Confirm product specifications at the time of order placement.
- Develop a Product Specification Sheet (PSS) and Inspection Specification Sheet (ISS) based on your needs and product requirements.
- Ensure the factory acknowledges and understands these specifications by obtaining their signatures.
2. Scheduling:
- Coordinate with the factory to determine a suitable inspection date.
- Align inspection dates with the shipping schedule and your QC department’s convenience.
- Confirm the inspection date with the factory and notify your QC department accordingly.
3. Documents and Tools:
Equip the QC inspector with necessary tools and documents, including:
- Product Specification Sheet
- Inspection Specification Sheet
- QC Inspection Checklist
- Drawings
- Purchase Order (PO) sent to the factory
- Packing labels
- Carton labels
- Any other relevant documents or tools required for inspection.
4. On-site Factory Inspection:
The QC inspector conducts a comprehensive on-site inspection following the ISS requirements, including:
- Using the QC Inspection Checklist as a step-by-step guide.
- Ensuring random sampling for quality verification.
- Recording all on-site data in a report form.
- Capturing clear product photos, including the details.
- Maintaining open communication with the sourcing team.
- If necessary, select production samples randomly for quality verification and certification.
5. Inspection Results:
- Complete the PSI report and send it to the buyer before packing and transportation.
- Include dimension sheets, photos, material certificates, factory QC pass certificates, and any other necessary documents to provide a comprehensive report, as required by the PO or the buyer.
In many cases, factories in China offer self-inspection services. However, it’s crucial to work with factories that have a well-established quality assurance system in place. Even if you have a longstanding relationship with a factory, conducting a thorough third-party PSI remains essential to ensure that your goods conform to your specifications and expectations.
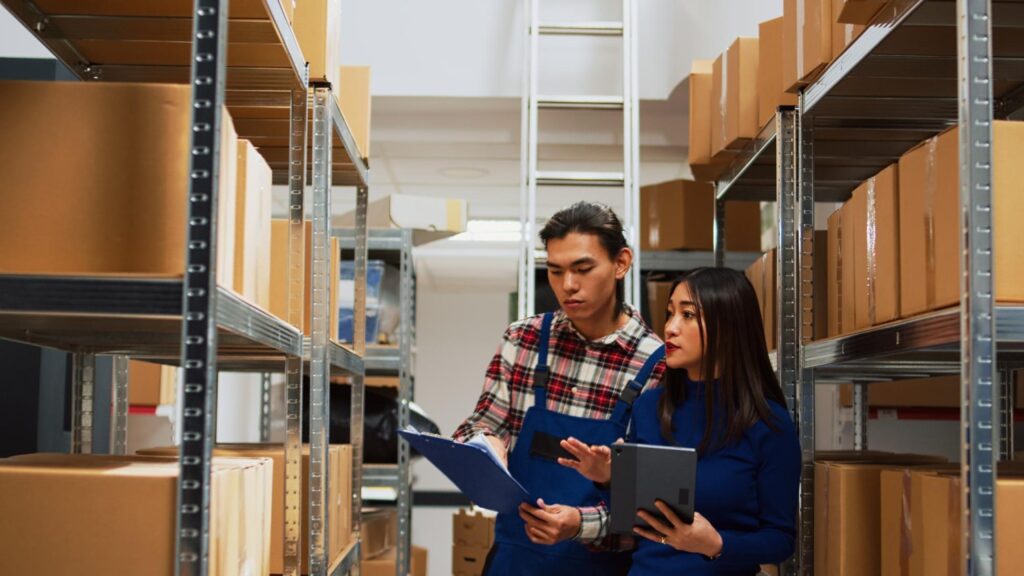
Mastering the Pre-shipment Inspection is a critical skill for successful China sourcing. By following the steps detailed above and maintaining a proactive approach to quality control, you can protect your business from potential quality problems and shipping delays.
This article is inspired by the expertise of Iris Zhou, a highly accomplished professional with a Master’s degree in Logistics Engineering from Beijing Jiaotong University.
For more information, please contact:
Karlheinz ZUERL – CEO of GTEC (German Technology & Engineering Cooperation)
- E-Mail: contact@gtec.asia
- Mobile: + 86 13482438080
Experts in the Automotive Industry Asia
You need one, but don`t want to hire one permanently?
Our solution: To rent our experts
- On pay-to-use basis
- Completely flexible
- Contract can be cancelled any time
Clearly represented reports and dashboards inclusive!