Project Purchaser in the engineering industry – aerospace industry
Market Research Specialist, Nanda Petroleum and Chemical Products Co. Ltd
Procurement Specialist, Alp Engineering Co. Ltd, Istanbul
Purchasing Manager, ewo – Hermann Holzapfel LLC, Stuttgart-Vaihingen
Purchasing/ Logistics Manager, awetis engineering + manufacturing Co. Ltd
Strategic Purchaser Electrotechnology and Deputy Head of Purchasing Department, Reifenhäuser Blown Film Co. Ltd.
Owner of Umit Gunay – Purchasing Consultancy and Mediation in sideline, main occupation since February 2023
Reifenhäuser Blown Film Co. Ltd. – interim mandate in the engineering industry
Broetje Automation GmbH – interim mandate in the engineering industry – building assembly lines in aerospace industry
University of Applied Sciences in Constance
Degree: Business-Sinologist (FH)
Key aspect: Chinese Language, Intercultural Communication, International Economics,
Project Management and Finance, Internationalization of Business Functions Global Cooperation
Digital Transformation – Leuphana University Luneburg – Diploma of Basic Studies
2nd party auditor (TUV) according to ISO 9001, ISO 19011 and ISO/TS 16949 (Seminar# 02-65)
Rhetoric training for purchasers
Waste management officer
University of Applied Sciences in Hamburg (HFH) – materials engineering (ZFU-Nr. 240208)
Next Level Purchasing – Supply Management Contract Writing
Next Level Purchasing – Savings Strategy Development
Next Level Purchasing – 14 Purchasing Best Practices
MS-Office
SAP S/4 HANA
Tacto: supplier onboading
Allex AI: plattform for project management
Onventis: plattform for all-in-one-procurement
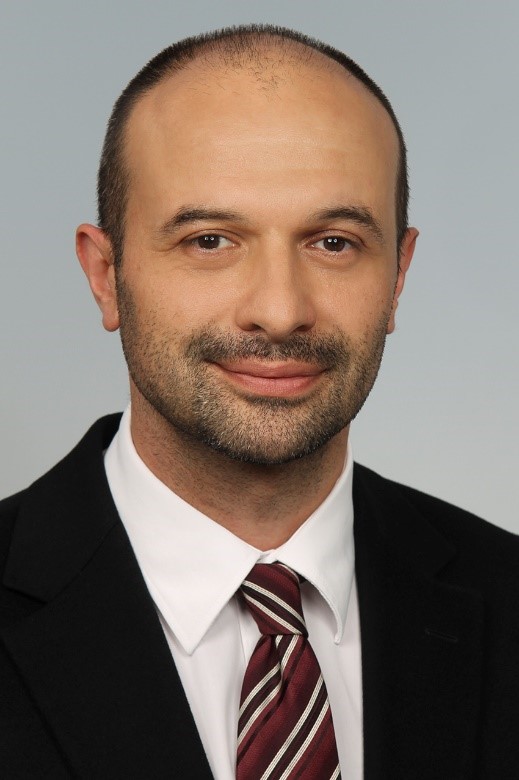
Nationalität: Deutsch
Wohnort: Germany
Position: Project Purchaser
Geburtsjahr: 1978
Sprachen: German (Native), English (Business fluent), Turkish (Business fluent), Chinese/Mandarin (Fluent)